Frank and his crew started the day drawing chalk lines between the pins set by the surveyor while waiting for the ICF block to be delivered. Unfortunately, the truck got lost and did not make it to the site until around 1300h. Once the truck arrived, they started setting block along the chalk line.
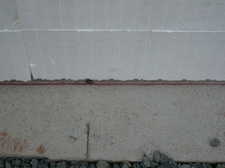
The basement is built using 8" ICF block. That is, 2.5" of foam, a space for 8" of concrete and then another 2.5" of foam. The rest of the house will be built using 6" block.
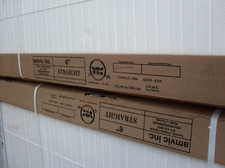
When necessary, the block can be cut using a utility knife.
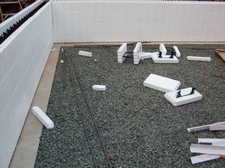
And, if there is a gap such as where the footer meets the block, it can be filled with expanding spray foam such as Foam2Foam.
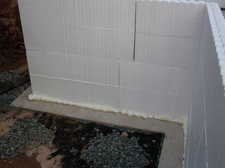
This is what the site looks like after they unloaded the tractor trailer of block and worked for about four hours setting block.
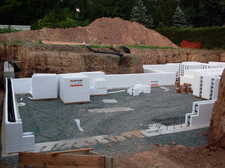
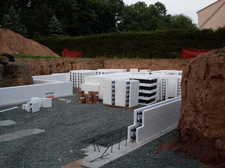
We can also finally start to see the footprint of the house. Walter had to overdig the hole for the basement and footers to leave room to work and drainage around the house, and then the footers themselves have to sit out beyond the basement walls in order to support the weight of the house. And the basement walls are 13" thick when you account for all the foam and concrete so the footprint gets significantly smaller, finally.
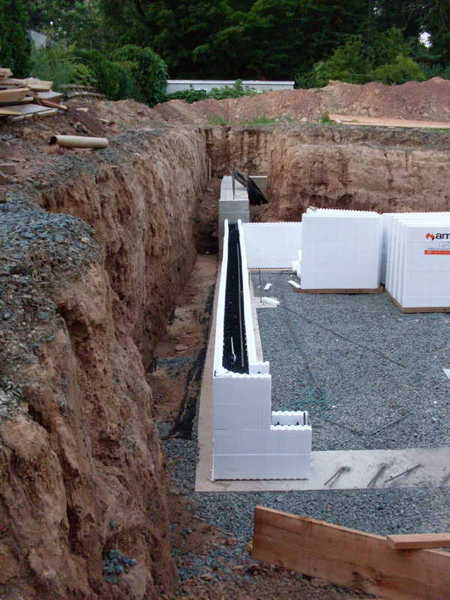
The vertical rebar sticking out of the footers will help hold the concrete for the walls to the concrete footers, while additional rebar is added to the ICF walls for lateral strength.
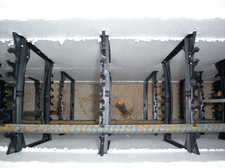
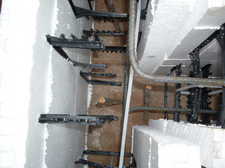
As we get to where the basement wall ends and the first floor will go, Frank and his crew will embed Simpson Strong-Tie connectors into the walls to support the floor above.
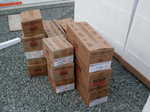
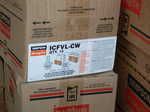
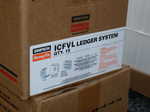
And, finally, before the space outside the basement walls is backfilled, Frank's crew will attach Platon membrane to assist with waterproofing the walls.
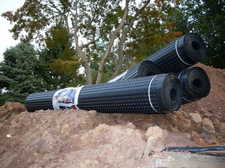
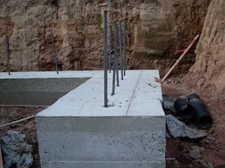
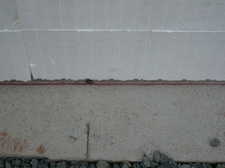
The basement is built using 8" ICF block. That is, 2.5" of foam, a space for 8" of concrete and then another 2.5" of foam. The rest of the house will be built using 6" block.
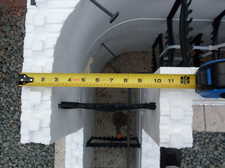
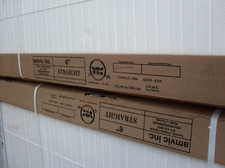
When necessary, the block can be cut using a utility knife.
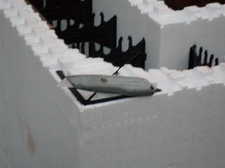
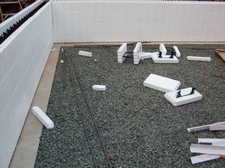
And, if there is a gap such as where the footer meets the block, it can be filled with expanding spray foam such as Foam2Foam.
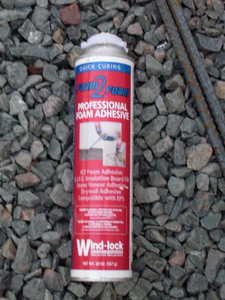
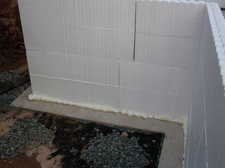
This is what the site looks like after they unloaded the tractor trailer of block and worked for about four hours setting block.
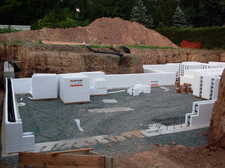
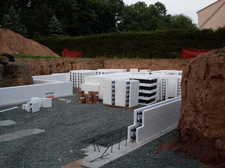
We can also finally start to see the footprint of the house. Walter had to overdig the hole for the basement and footers to leave room to work and drainage around the house, and then the footers themselves have to sit out beyond the basement walls in order to support the weight of the house. And the basement walls are 13" thick when you account for all the foam and concrete so the footprint gets significantly smaller, finally.
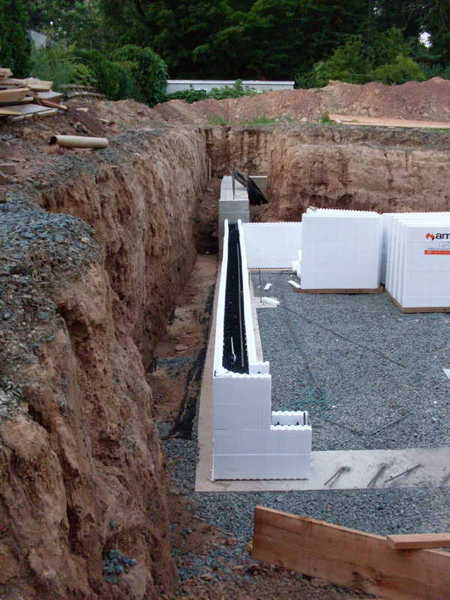
The vertical rebar sticking out of the footers will help hold the concrete for the walls to the concrete footers, while additional rebar is added to the ICF walls for lateral strength.
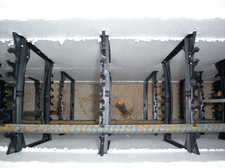
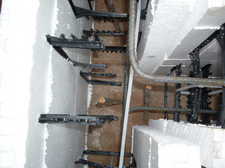
As we get to where the basement wall ends and the first floor will go, Frank and his crew will embed Simpson Strong-Tie connectors into the walls to support the floor above.
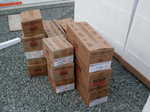
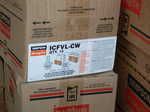
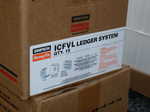
And, finally, before the space outside the basement walls is backfilled, Frank's crew will attach Platon membrane to assist with waterproofing the walls.
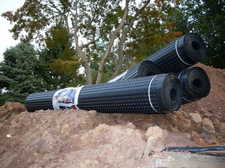
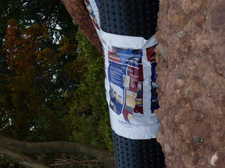
Leave a comment