Well, it has been almost three months since my last entry. That's not because work stopped -- it did not. But I've been busy and a lot of the work wasn't easy to photograph without being in the way (during the day, while work was in progress) or couldn't be photographed (at night, without light in the house).
We did loose sometime due to the weather, unfortunately. We had hoped to pour the concrete for the garage floor and front porch but that did not happen due to the multiple blizzards and ice storms. And we lost a few days as everyone was busy digging themselves out of the storm, or Victor had to get the job site dug out so everyone else had access again. They did finish the Duradek patio in front and back (though no railings are up) but I never got a chance to take a picture before it got buried in snow.
The rough HVAC work (supply & return ducts, and the equipment) is installed and pictures will follow soon. The drilling for the geothermal wells could happen as soon as this week. The rough plumbing is virtually complete and the rough electric has begun. Fire sprinklers will hopefully start this week as will the low voltage work (fire & security system, whole house audio, and conduit for future data, telephone & television wiring).
But, the stucco installers persevered. On the days before it got very cold, the installed the foam trim pieces and basecoat of the stucco. Then, when it got cold, they tarped the whole house and setup propane heaters under the tarp to keep things warm. I'm told that, on the upper levels of the scaffolding, you would still be sweating while wearing just a T-shirt, even if it was below freezing outside.
I have to admit - I kinda liked the blue house better than the finished product. It covered up all the pesky windows the architects added.
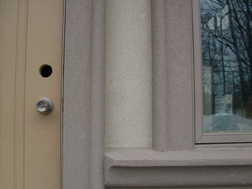
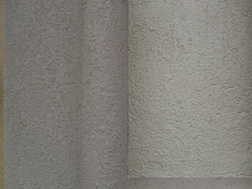
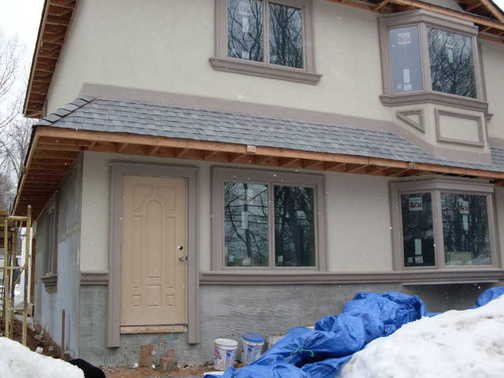
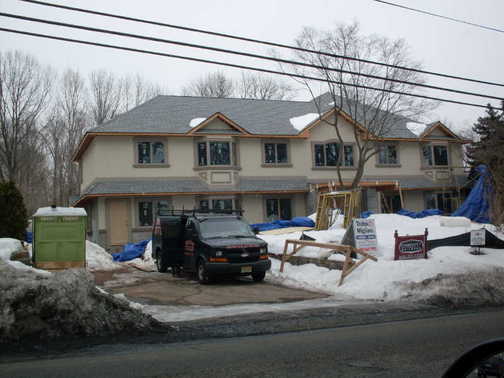
Recent Comments