Okay, maybe more than twice.
We had to get a survey before we bought the property. Then we needed an updated boundary and topographic survey to finalize where the house sat on the property.
Next, the surveyors came back to set stakes indicating where we needed to excavate. After the initial excavation, Victor and Chrispin (Conquest Builders) measured where the piers would go and Walter (Heckel Excavators) dug that out as well.
But, now the surveyors are back to mark the exact location of all the corners before the masons come.
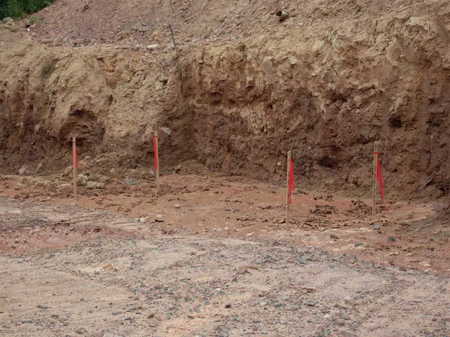
By the way, in case you were wondering what an insulated concrete form (ICF) block looks like, we have a sample. This particular one is a 6" Amvic ICF block. The black spot in the first picture is where some of the foam has been removed to reveal the plastic web inside. To give you some perspective, a dollar bill (approx. 2.61" x 6.14") and a quarter (0.955") are also shown.
The ICF block is composed of two expanded polystyrene (EPS) boards, 16 inches high by 48 inches long, and come with 4, 6, 8 or 10 inches between each board which gets filled with concrete. (The 10 inch core block is 24 inches high.) Each foam board is 2.5 inches thick and they are joined by plastic webs placed every 6 inches. (After installation, we can nail or screw things into these plastic webs, just as you would normally fasten to a wooden stud.) The top and bottom of each board has foam "pegs" (1" square and spaced 1" apart) so that the blocks can lock to each other just like Lego blocks.
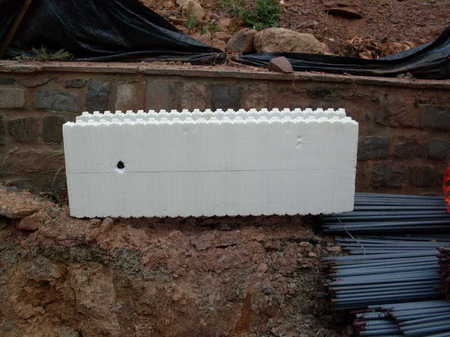
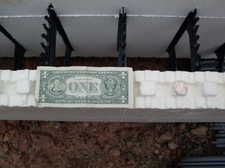
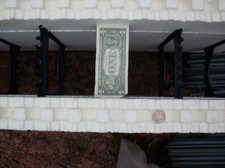
Finally, in case you were wondering, mom's garden is doing just fine. Of course, getting to it is a little difficult for her but its feeding some of the local wildlife just fine.
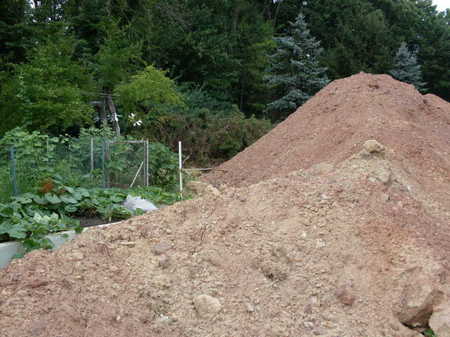